Ultrasonic Atomization
Ultrasonic spraying is a method of liquid dispersion in which high-frequency ultrasound generates fine droplets. This technology has advantages over conventional spraying methods, including more uniform particle size, higher energy efficiency, and less waste.
Have questions about any of our products listed below? Looking for a quote or more info? Contact us via the menu above or the link at the bottom of this page.
Standard OEM Ultrasonic Modules
Low-Frequency Ultrasonic nozzles
Operating in the frequency range of 20 kHz to 100 kHz, these nozzles utilize a vibrating ultrasonic surface to atomize liquids into droplets with controlled particle sizes. Small in size, our spray nozzles are provided in OEM Modules and are used for a variety of applications.
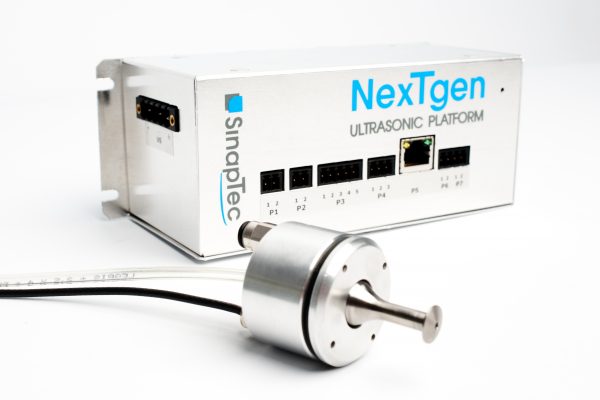
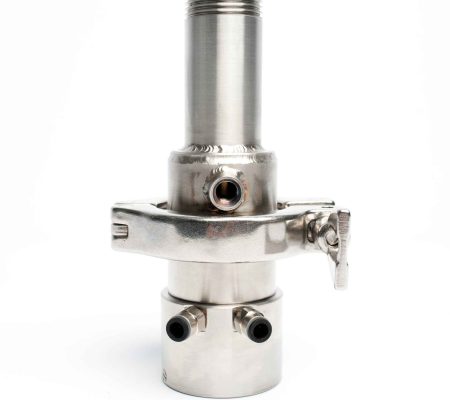
High-Frequency Ultrasonic Atomizers
These systems function at frequencies around 100 kHz and use an ultrasonic emitter placed at the base of a liquid reservoir. The acoustic field generates a liquid fountain, forming an aerosol at its surface. Our aerosol generators are offered as OEM modules.
Benefits of Ultrasonic Spraying
-
Uniform Particle Size:
Ultrasonic technology produces droplets of uniform size that are applied efficiently for higher coating quality.
-
Energy Efficiency:
Compared to conventional methods, ultrasonic spraying requires less energy, reducing operational costs.
-
Waste Reduction:
The fine droplets generated by ultrasounds help improve liquid absorption, minimizing waste.
-
Versatility:
Ultrasonic spraying can be applied in various fields, such as the food, pharmaceutical, and cosmetic industries.
Applications of Ultrasonic Spraying
Ultrasonic spraying is employed across numerous industries. It is widely used in the paint and coatings industry, enabling the application of thin and uniform layers on objects of all shapes and sizes. Such industries include:
-
Pharmaceutical Industry:
Used in drug manufacturing processes.
-
Electronics Industry:
used to deposit conductive or insulate materials on printed circuit boards.
-
Food Industry:
used to apply protective coatings on products, extending shelf life.
Thanks to its precision and efficiency, ultrasonic spraying is a versatile technology that is finding increasing applications in sectors such as aerospace, energy, and many others.
Notable Use Cases
-
Coatings:
Ultrasonic spraying creates thin, even layers on surfaces that improve protective and aesthetic properties.
-
Inhalers:
Ultrasonic spraying is used in inhalers to deliver medication in fine droplets into the respiratory tract for rapid absorption and action.
-
Humidification:
Ensures consistent and fine water dispersion in industrial, agricultural, and residential settings.
-
Airborne Surface Disinfection (ASD):
Distributes disinfectants as aerosols for thorough coverage in enclosed spaces.
-
Aroma Diffusion:
Our nozzles help to disperse fragrances and aromatic products, enhancing ambiance in wellness spaces, events, and commercial settings.
-
Tracer Production:
In industrial and scientific processes, our nozzles are used to spray liquid tracers that assist in detecting and analyzing flows, leaks, or fluid movements.
-
Confined Space Atmospheric Controls:
It is used to regulate the atmospheric conditions in confined spaces such as cleanrooms, laboratories and any other sensitive production areas.
-
Thin-Film Deposition:
Used in manufacturing processes that require the precise application of thin layers of liquid materials on various surfaces, such as in the electronics industry, optical coatings, and specialized paints.
-
Ultrasonic Spray in Drying Processes:
Spray drying is a very efficient way of converting solutions or suspensions into powders or granules without having to go through other processes like evaporation or grinding. With the help of ultrasonic atomization, the suspensions are uniformly dispersed into micrometric or submicrometric droplets, which are then dried in the spray dryer using hot air. The method generates smaller and more consistent particles than conventional approaches and has many promising applications in nanomaterials, fine chemistry, and biomedicine.
Factors Affecting Ultrasonic Spraying Efficiency
Several factors influence the effectiveness of ultrasonic spraying:
- Frequency plays a critical role. The higher the ultrasonic frequency, the finer the droplets. The choice of frequency depends on the application and the required particle size.
- The viscosity of the liquid can affect the efficiency of ultrasonic spraying. For highly viscous liquids, specific adaptations to the equipment and the spraying process may be necessary.
- The distance between the nozzle and the target surface can greatly impact the effectiveness of ultrasonic spraying. This is particularly true for applications requiring precision on small surfaces.
The design and quality of the components of the ultrasonic nozzle can also impact the spraying efficiency. High-quality components lead to better performance and equipment longevity. It is very important to verify the compatibility of the nozzle materials with the liquid being sprayed.
In Summary
Ultrasonic spraying is an innovative technology that offers many advantages across different industrial sectors. This method allows for fine and uniform dispersion of liquids, enhances energy efficiency, and minimizes waste. Contact us to integrate ultrasonic spraying into your processes, improve product quality, and optimize outcomes.