Ultrasound: General Principles of ultrasonic waves
Ultrasound, those sound waves whose frequencies are too high for the human ear to perceive, has undergone many advances over the years, culminating in the applications we know today. On this page, after a brief historical review, we take a look at some of the general principles governing the fascinating world of ultrasound.
What is ultrasound?
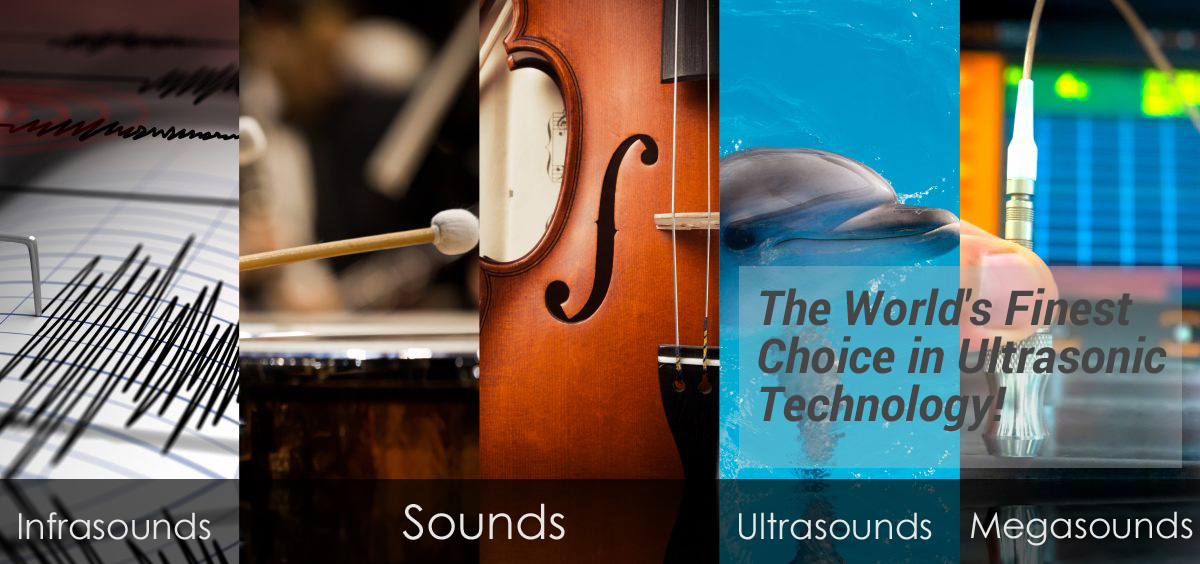
Ultrasound Definition
Ultrasound is a vibration similar to sound, but with a much higher frequency, making it imperceptible to the human ear. Ultrasound is an elastic wave whose frequency ranges from around 16 kHz to several hundred Megahertz. As you can see from the illustration above, the frequency range audible to the human ear, sounds, is preceded by infrasound and followed by ultrasound and megasonics.
History of Ultrasound
Frenchman Paul Langevin carried out the first work on ultrasound production techniques for SONAR at the end of the First World War. The applications and industrial uses of ultrasound developed towards the end of the 1950s. At this time a number of laboratories also demonstrated the extreme diversity of the applications of ultrasound.
Some of this work led rapidly to applications in the area of medical diagnostics and control, whilst aside from cleaning and welding, the use of high-power ultrasound in industry was not as widely spread. During the 1980s, the rapid development of modelling techniques led to significant progress being made in ultrasound technology.
Types of ultrasound applications
Developments in electronics have greatly improved the performance of ultrasonic equipment, opening up new prospects for its use in industry. These applications of ultrasound are generally classified into two categories:
-
Low-power ultrasound:
The first category, low-power ultrasound, is mainly used in diagnostics, measurement and control. They allow analysis and monitoring without altering the environment being examined, making them invaluable tools for precise, non-invasive inspections.
-
High-power ultrasound:
The second category, high-power ultrasound, is defined by its ability to physically modify the environment in which it propagates. Its effects can be mechanical, thermal or chemical, making it particularly effective in demanding industrial applications. For example, when applied to solid materials, ultrasound can generate heating, as in the welding process, or induce vibrations that change the apparent coefficient of friction, or clean screens by unclogging them. These capabilities illustrate the versatility and effectiveness of high-powered ultrasound in a wide range of industrial operations.
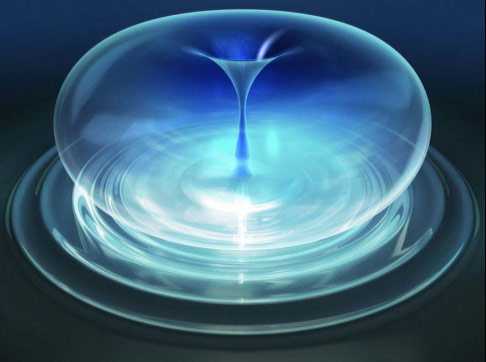
-
Ultrasound in fluids :
Cavitation is the predominant phenomenon generated by ultrasound and plays an essential role in many industrial scientific applications. This process is produced by emitting intense ultrasound waves which create areas of alternate compression and dilation. Above a certain threshold, they induce the implosion of micro-bubbles causing a significant localised heat increase and a wave of pressure several thousand times greater than atmospheric pressure.
These cavitation effects are exploited in a wide variety of industrial processes and laboratory techniques. These include surface cleaning and treatment, as well as advanced processes such as dispersion, homogenization, particle size reduction, plant extraction or eco-extraction (essential oils, microalgae, cannabis, polyphenols, etc.), cell disruption, sonochemistry, etc.)
In the more specific field of liquid treatment, ultrasonic applications go far beyond simple cleaning. Often referred to as “ultrasonic fluid processing,” this field encompasses a variety of techniques that alter the properties of fluids in a controlled manner to achieve precise, effective results. These technologies use the power of ultrasound to change the physical, chemical or biological properties of fluids, opening the door to innovation in many industrial and research sectors.
-
Les Ultrasons dans les poudres :
Ultrasound has a remarkable effect on powders, offering significant advantages in their production, handling and processing. These specific ultrasonic effects help to optimize various industrial processes related to powders.
One of the advantages of using ultrasound is its ability to reduce the clogging of screens. This property is particularly beneficial when sieving fine powders, where ultrasound improves efficiency by preventing the build-up of particles that could clog the mesh. Another valuable application is the production of powders by ultrasonic atomization. This technique reduces the dispersion of the particle diameters produced, resulting in a significant increase in production yield.
Another advantage is that ultrasonic surface excitation provides highly effective unclogging by facilitating particle detachment. This method is often used to remove obstructions in hoppers and pipelines clogged with dry deposits.
Finally, ultrasonic powder compaction is an innovative technique for increasing the density of sintered materials. The use of ultrasound in this context helps to achieve a denser, more homogeneous material, thus improving the quality and mechanical properties of the final product.
-
Ultrasounds in gas :
The use of ultrasound over short distances offers the possibility of generating very intense acoustic fields, opening the way to a number of practical applications in the processing of liquids and powders. These powerful acoustic fields are particularly effective for spraying liquids, dispersing powders and agglomerating particles, techniques often required in industrial processes that require precise handling of materials.
The application of ultrasound also extends to defoaming processes, such as in the food industry when filling containers such as bottles and cans, especially for beer and dairy products. Ultrasound facilitates this process by reducing foaming, thereby speeding up the filling process.
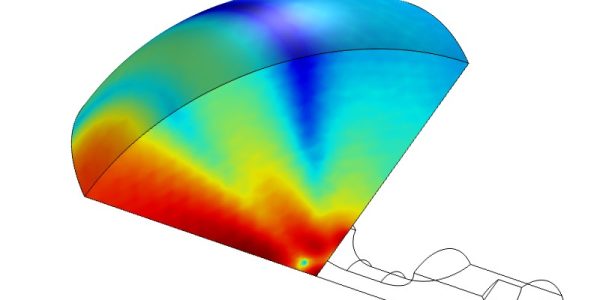
-
Ultrasound in solids (warmth, vibration):
When ultrasound is used to vibrate a material, a number of physical phenomena occur, of which heating is particularly noticeable. This phenomenon results from the absorption of the vibratory wave by the material, transforming the acoustic energy into heat. Such heating plays a fundamental role in certain industrial applications, notably in the welding of thermofusible materials such as plastics, plastic films and technical textiles.
Metal welding also benefits from the principles of ultrasonic vibration. This method involves the vibration of two metal parts to be joined, combined with the application of high pressure. A major advantage of this technique is that welding takes place below the melting temperature of the materials involved. As a result, the structural properties of the metals are less likely to be compromised.
The diversity of ultrasonic applications is so vast that it is difficult to draw up an exhaustive list. Ultrasound must be seen as a particular form of energy, whose properties and benefits vary greatly according to the methods and contexts in which it is employed.
High-power ultrasound
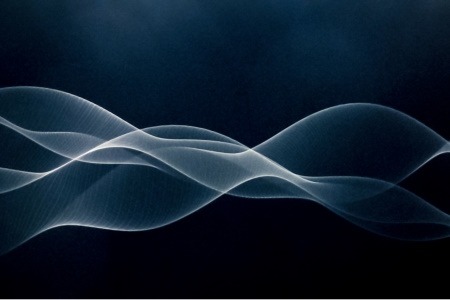
Ultrasound applications are developing in all fields, drawing on the results of over 70 years of research. Discover high-power ultrasound.