Do you have a question about any of the products below? Need a quote or more information?
Introduction
Our ultrasonic defoaming technology is particularly well-suited for bottling and canning lines in the beverage, brewing, dairy, and chemical industries.
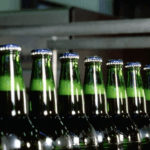
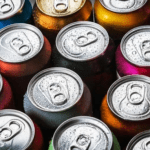
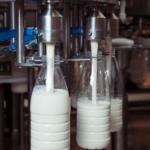
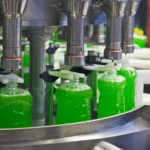
Advantages of Ultrasonic Defoaming
Undesirable foam formation is typically managed using mechanical devices, lowering liquid temperatures, or adding chemical additives. However, these methods can have limitations.
Ultrasonic defoaming systems, by contrast, have proven highly effective at eliminating foam. Ultrasonic waves travel through the air, creating cycles of pressure and decompression leading to the implosion of larger bubbles and the compression of finer ones within the vessel.
Key benefits of ultrasonic defoaming include but are not limited to:
- Increased productivity: Faster filling speed, extremely low maintenance and cleaning time.
- Production efficiency: Reduced product loss and lower rejection rates (cans or bottles).
- Waste reduction: Less water and fewer chemicals used for line cleaning.
- Energy savings: Higher product temperature which reduces refrigeration costs. An ultrasonic generator consumes approximately 100W continuously.
- Improved hygiene and quality: Lower microbiological risks on caps, seals, and packaging.
- Excellent ROI: Based on production rates, ROI can be less than one month.
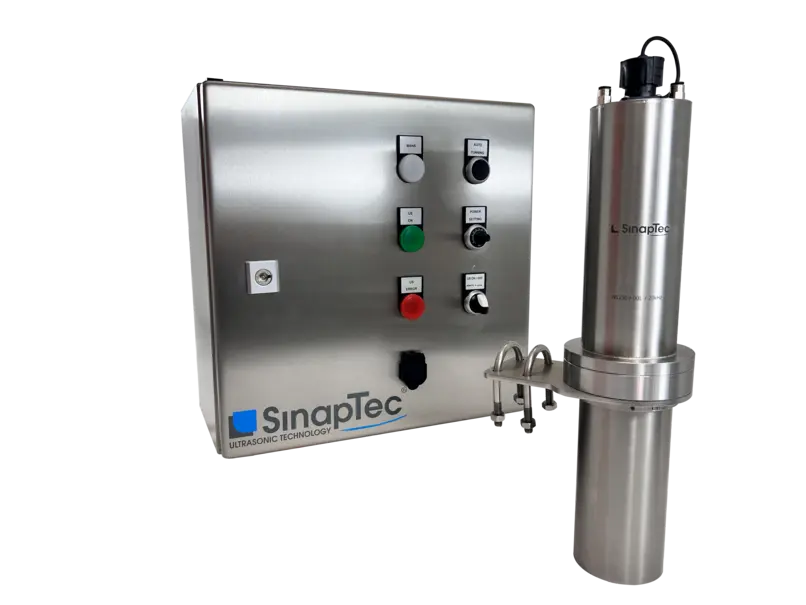
For operators of bottling lines struggling to maximize production capacities, we offer a ready-to-install turnkey solution requiring less than 60 minutes of downtime.
The ultrasonic generator is kept in a stainless-steel IP66-rated cabinet, while the defoaming acoustic system is designed and ready to be positioned above the line.
Ultrasonic Nozzle (20 or 30kHz) for Ultrasonic Defoaming
We specialize in designing, manufacturing, and providing standard, modified, and custom ultrasonic modules, including generators and transducers.
For machine manufacturers and integrators, our ultrasonic generator is designed to be incorporated into electrical cabinets. It features input/output interfaces for fast system control (start/stop, faults, amplitude, autotuning, system status, etc.) and includes a ModBus TCP port for seamless integration.
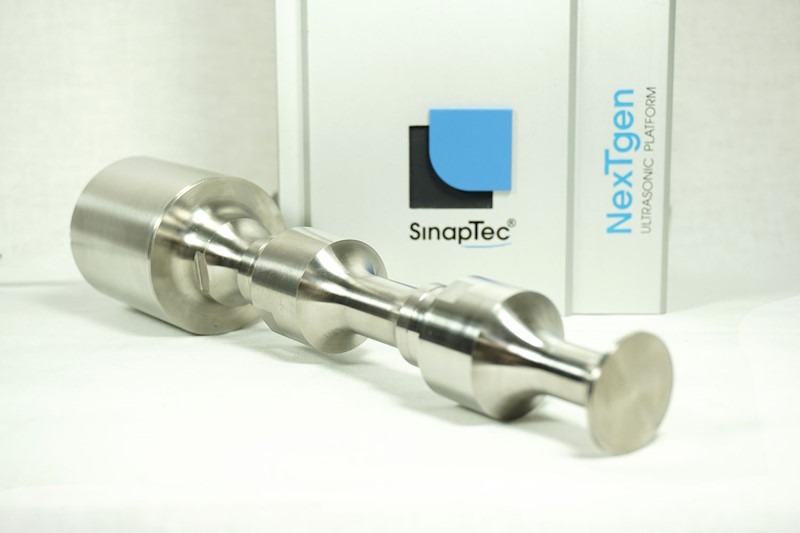
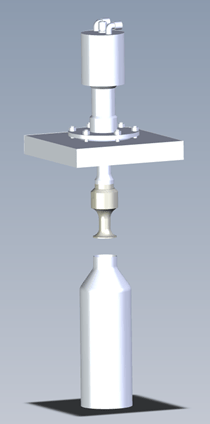
Custom Ultrasonic Nozzle for Ultrasonic Defoaming
Are our standard OEM products not meeting your requirements (e.g., space constraints, power requirements)? Know that our R&D team is here to develop tailored solutions to meet your needs.
Our ultrasonic nozzle is built with high-quality materials like titanium and stainless steel to ensure optimal durability. It can operate at either 20 or 30 kHz, depending on the model.
Similarly, we also offer a version tailored for aseptic filling lines:
- Electropolished surfaces
- Minimal retention areas
- Easy cleaning
- Hygienic and polished weld seams
Case Study – Optimizing Ultrasonic Defoaming on a Brewery Filling Line
Location: Europe
Objective: Increase line speed using ultrasonic defoaming
Initial Setup: A brewery was filling 330ml bottles at 36,000 bottles per hour (bph) on a KHS mechanical filler. Products were blonde and amber ale. Excess foam formation was observed before capping, forcing them to reduce filling speeds by 10% in order to prevent overflows and product loss.
OEM Ultrasonic Solution: SinapTec delivered a full ultrasonic defoaming system (acoustic assembly and electrical cabinet) ready for installation. Positioning it 20cm before the high-pressure jet allowed a maximum production capacity of 40,000 bph.
The transducer/sonotrode was installed on the filling line in just 60 minutes, minimizing production downtime. On the other hand, the electrical cabinet was set up beforehand in only 2 hours, thanks to prior technical discussions with the client’s engineer.
Results: By implementing SinapTec’s ultrasonic defoaming unit, the brewery achieved:
- Increased filling speed from 36,000 to 40,000 bph.
- Reduced product loss before capping.
- Maintained Total Package Oxygen (TPO) levels.
Key Metrics:
- Improvement: Line speed increased by 10% (36,000 to 40,000 bph).
- Estimated Annual Volume: 10% production increase i.e. 16,000,000 additional bottles/year at €0.12/bottle. (based on an annual production of 4,000 hours/year).
- Estimated Gains: €960,000/year
- ROI: Less than one month.
How Ultrasonic Defoaming Works
Ultrasonic technology generates an acoustic wind effect in front of the probe without any gas displacement.
The focused acoustic waves create a pressure field of a few centimeters in front of the probe, effectively breaking or compressing foam that may form during filling. This results in compressed, denser foam inside the container, significantly boosting efficiency and productivity.
Applications of Ultrasonic Defoaming Across Key Sectors
– Brewing
Carbonation during beer production causes significant foam during bottling. Ultrasonic defoaming helps control foam and optimize filling speeds while minimizing product loss and preserving beer quality.
– Beverages
Foam is a common issue during high-speed filling of carbonated and non-carbonated drinks. Our ultrasonic nozzles effectively minimize foam, ensuring faster filling and reduced product loss for sodas, sparkling water, and juices.
– Dairy
Foam during dairy product filling can slow operations. Ultrasonic defoaming ensures precise filling, strict hygiene compliance, and easier cleaning, which is a key requirement for the dairy industry. It also facilitates the sealing process by reducing residues on the container.
– Chemicals
In the chemical industry, products like solvents and cleaning agents often produce foam during filling. Our ultrasonic technology provides a non-invasive solution to control foam without requiring chemical additives, ensuring a safe and clean packaging process while maintaining the product’s chemical integrity.
Summary
Ultrasonic defoaming is an ideal innovative solution for managing foam in various industries, such as the brewing, beverage, dairy, and chemical sectors. By using ultrasonic nozzles, this technology efficiently reduces foam during filling, enhancing production speed and minimizing product loss. Unlike traditional methods, ultrasounds maintain the product’s integrity and adhere to strict hygiene standards, making it a perfect choice for boosting productivity and quality in demanding environments.